Calibração de Válvula de Segurança: Como Garantir a Eficiência e Segurança do Seu Sistema
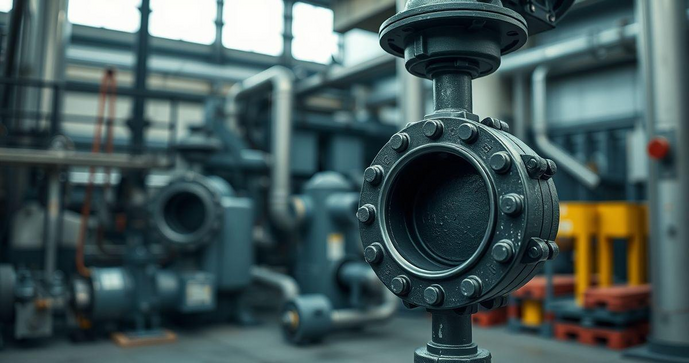
Por: Walter - 24 de Março de 2025
A calibração de válvula de segurança é um procedimento crucial para garantir a eficiência e a segurança em sistemas industriais. Este processo assegura que as válvulas funcionem corretamente, evitando falhas que podem resultar em acidentes graves. Neste artigo, abordaremos a importância da calibração, o passo a passo para realizá-la, os erros comuns a serem evitados e a necessidade de manutenção regular para garantir o desempenho ideal das válvulas de segurança.
Importância da Calibração de Válvula de Segurança para a Segurança Operacional
A calibração de válvula de segurança é um aspecto fundamental na operação de sistemas industriais, especialmente em setores que lidam com substâncias perigosas ou que operam sob alta pressão. A função principal dessas válvulas é proteger equipamentos e instalações contra sobrepressões, evitando acidentes que podem resultar em danos materiais, lesões ou até mesmo fatalidades. Portanto, a calibração adequada dessas válvulas é essencial para garantir a segurança operacional.
Um dos principais motivos para a calibração de válvulas de segurança é a necessidade de garantir que elas funcionem dentro dos parâmetros especificados pelo fabricante. Com o tempo, as válvulas podem sofrer desgastes ou alterações em suas características, o que pode comprometer sua capacidade de abrir e liberar pressão excessiva. Se uma válvula não for calibrada corretamente, pode não abrir quando necessário, resultando em uma pressão excessiva que pode danificar equipamentos e causar acidentes.
Além disso, a calibração regular das válvulas de segurança é uma exigência normativa em muitos setores. Normas como a NR-13, que regulamenta a segurança em caldeiras e vasos de pressão, estabelecem que as válvulas de segurança devem ser testadas e calibradas periodicamente. O não cumprimento dessas normas pode resultar em penalidades legais e, mais importante, em riscos à segurança dos trabalhadores e do ambiente.
Outro ponto a ser considerado é que a calibração de válvulas de segurança contribui para a eficiência operacional. Quando as válvulas estão calibradas corretamente, elas ajudam a manter a pressão dentro dos limites desejados, evitando flutuações que podem afetar o desempenho dos equipamentos. Isso não apenas melhora a eficiência do sistema, mas também prolonga a vida útil dos equipamentos, reduzindo custos com manutenção e substituição.
Além da segurança e eficiência, a calibração de válvulas de segurança também é crucial para a proteção do meio ambiente. Em indústrias que lidam com substâncias químicas perigosas, uma falha na válvula de segurança pode resultar em vazamentos que podem contaminar o solo e a água, causando danos irreparáveis ao meio ambiente. A calibração adequada ajuda a prevenir esses incidentes, garantindo que as válvulas funcionem corretamente e que os sistemas de contenção estejam em pleno funcionamento.
Para realizar a calibração de válvulas de segurança, é importante utilizar equipamentos adequados e seguir procedimentos estabelecidos. O uso de tecnologias como o Ultrassom industrial pode ser uma solução eficaz para verificar o funcionamento das válvulas. Essa tecnologia permite a detecção de vazamentos e a análise do desempenho das válvulas sem a necessidade de desmontá-las, o que economiza tempo e recursos.
Além disso, a calibração deve ser realizada por profissionais qualificados, que tenham conhecimento sobre os equipamentos e as normas de segurança aplicáveis. Esses profissionais devem ser capazes de identificar problemas potenciais e realizar ajustes necessários para garantir que as válvulas estejam operando de maneira eficaz.
Outro aspecto importante é a documentação dos processos de calibração. Manter registros detalhados das calibrações realizadas, incluindo datas, resultados dos testes e quaisquer ajustes feitos, é fundamental para garantir a conformidade com as normas e para facilitar auditorias futuras. Essa documentação também pode ser útil para identificar tendências de desgaste e para planejar manutenções futuras.
Por fim, a calibração de válvulas de segurança deve ser parte de um programa abrangente de manutenção preventiva. Isso significa que, além da calibração, as válvulas devem ser inspecionadas regularmente para identificar sinais de desgaste ou danos. A combinação de calibração regular e inspeções pode ajudar a garantir que as válvulas de segurança funcionem corretamente e que os sistemas operacionais permaneçam seguros e eficientes.
Em resumo, a calibração de válvula de segurança é um componente crítico da segurança operacional em ambientes industriais. Ela não apenas protege os trabalhadores e os equipamentos, mas também contribui para a eficiência e a proteção ambiental. Investir em calibração regular e em tecnologias avançadas, como o Ultrassom industrial, é uma decisão inteligente que pode resultar em operações mais seguras e sustentáveis.
Passo a Passo para Realizar a Calibração de Válvula de Segurança
A calibração de válvulas de segurança é um procedimento essencial para garantir a segurança e a eficiência operacional em sistemas industriais. A seguir, apresentamos um guia passo a passo para realizar a calibração de válvulas de segurança, assegurando que elas funcionem corretamente e atendam às normas de segurança aplicáveis.
1. Preparação e Planejamento
Antes de iniciar o processo de calibração, é fundamental realizar um planejamento adequado. Isso inclui a identificação da válvula a ser calibrada, a coleta de informações sobre suas especificações técnicas e a revisão das normas aplicáveis, como as Inspeções nr13. Além disso, é importante reunir todos os equipamentos e ferramentas necessárias, como manômetros, chaves de fenda, e, se necessário, um sistema de ultrassom para verificar o funcionamento da válvula.
2. Desligamento do Sistema
Antes de realizar qualquer trabalho na válvula de segurança, é crucial desligar o sistema em que ela está instalada. Isso garante a segurança do operador e evita acidentes. Certifique-se de que a pressão do sistema esteja completamente liberada e que não haja risco de vazamentos. Utilize procedimentos de bloqueio e etiquetagem para garantir que o sistema permaneça desligado durante todo o processo de calibração.
3. Inspeção Visual da Válvula
Com o sistema desligado, inicie uma inspeção visual da válvula de segurança. Verifique se há sinais de desgaste, corrosão ou danos visíveis. Preste atenção especial às conexões, vedantes e componentes móveis. Se houver qualquer sinal de dano, a válvula pode precisar de reparos ou substituição antes da calibração.
4. Conexão do Manômetro
Após a inspeção, conecte um manômetro à válvula de segurança. O manômetro deve ser capaz de medir a pressão de forma precisa e deve ser calibrado antes do uso. A conexão deve ser feita de forma segura para evitar vazamentos. Certifique-se de que o manômetro esteja posicionado corretamente para que as leituras sejam precisas durante o teste.
5. Ajuste da Pressão de Atuação
Com o manômetro conectado, inicie o processo de ajuste da pressão de atuação da válvula. Gradualmente, aumente a pressão do sistema até que a válvula de segurança comece a abrir. A pressão em que a válvula se abre deve estar de acordo com as especificações do fabricante. Se a válvula abrir em uma pressão diferente, será necessário ajustar a configuração da válvula.
6. Teste de Funcionamento
Uma vez que a válvula tenha sido ajustada, é importante realizar um teste de funcionamento. Aumente a pressão até o ponto de abertura da válvula e observe se ela se abre e fecha corretamente. O manômetro deve indicar a pressão em que a válvula se abre. Se a válvula não funcionar como esperado, pode ser necessário realizar ajustes adicionais ou verificar se há obstruções que impeçam seu funcionamento adequado.
7. Documentação dos Resultados
Após a calibração, é fundamental documentar todos os resultados obtidos durante o processo. Registre a pressão de abertura, quaisquer ajustes realizados e as condições da válvula antes e depois da calibração. Essa documentação é importante para garantir a conformidade com as normas de segurança e para facilitar futuras inspeções e manutenções.
8. Reinstalação e Teste Final
Depois de concluir a calibração e a documentação, reinstale a válvula de segurança no sistema. Certifique-se de que todas as conexões estejam seguras e que não haja vazamentos. Em seguida, realize um teste final do sistema para garantir que a válvula funcione corretamente em condições operacionais normais. Monitore a pressão e verifique se a válvula abre e fecha conforme esperado.
9. Manutenção Regular
A calibração de válvulas de segurança não deve ser um evento isolado. É importante estabelecer um cronograma de manutenção regular que inclua inspeções e calibrações periódicas. Isso garantirá que as válvulas permaneçam em boas condições de funcionamento e que atendam às normas de segurança. A manutenção regular também pode ajudar a identificar problemas antes que se tornem críticos, evitando falhas no sistema.
Em resumo, a calibração de válvulas de segurança é um processo que requer atenção aos detalhes e um planejamento cuidadoso. Seguir este passo a passo ajudará a garantir que as válvulas funcionem corretamente, contribuindo para a segurança operacional e a eficiência dos sistemas industriais. A calibração regular e a documentação adequada são essenciais para manter a conformidade com as normas e para garantir a segurança de todos os envolvidos nas operações industriais.
Erros Comuns na Calibração de Válvula de Segurança e Como Evitá-los
A calibração de válvulas de segurança é um procedimento crítico para garantir a segurança e a eficiência operacional em sistemas industriais. No entanto, existem diversos erros que podem ocorrer durante esse processo, comprometendo a eficácia das válvulas e colocando em risco a segurança dos trabalhadores e das instalações. A seguir, discutiremos os erros mais comuns na calibração de válvulas de segurança e como evitá-los.
1. Falta de Planejamento Adequado
Um dos erros mais frequentes na calibração de válvulas de segurança é a falta de planejamento. Muitas vezes, os profissionais iniciam o processo sem uma compreensão clara das especificações da válvula ou das normas aplicáveis. Para evitar esse erro, é fundamental realizar uma pesquisa prévia sobre a válvula, suas características e os requisitos normativos, como a Calibração de manometros e as diretrizes da NR-13. Um planejamento adequado garante que todos os passos necessários sejam seguidos e que os resultados sejam confiáveis.
2. Ignorar a Inspeção Visual
Outro erro comum é pular a inspeção visual da válvula antes da calibração. A inspeção visual é crucial para identificar sinais de desgaste, corrosão ou danos que podem afetar o desempenho da válvula. Ignorar essa etapa pode resultar em falhas durante a calibração e, consequentemente, em problemas operacionais. Para evitar esse erro, sempre realize uma inspeção detalhada antes de iniciar o processo de calibração, verificando todas as partes da válvula e suas conexões.
3. Uso de Equipamentos Não Calibrados
Utilizar manômetros ou outros equipamentos de medição que não estão calibrados corretamente é um erro que pode comprometer toda a calibração da válvula de segurança. Se os instrumentos de medição não estiverem precisos, as leituras obtidas durante a calibração podem ser incorretas, levando a ajustes inadequados. Para evitar esse problema, sempre verifique a calibração dos instrumentos antes de usá-los e, se necessário, realize a calibração de manômetros e outros dispositivos de medição antes do procedimento.
4. Não Seguir as Especificações do Fabricante
Cada válvula de segurança possui especificações únicas definidas pelo fabricante, incluindo a pressão de abertura e os métodos de ajuste. Ignorar essas especificações pode resultar em uma calibração inadequada. Para evitar esse erro, sempre consulte o manual do fabricante e siga as diretrizes fornecidas. Isso garantirá que a válvula seja calibrada corretamente e funcione conforme esperado.
5. Falta de Documentação
A documentação é uma parte essencial do processo de calibração, mas muitas vezes é negligenciada. Não registrar os resultados da calibração, os ajustes realizados e as condições da válvula pode levar a problemas futuros, especialmente durante auditorias ou inspeções. Para evitar esse erro, mantenha registros detalhados de cada calibração, incluindo datas, resultados e quaisquer observações relevantes. Essa documentação é fundamental para garantir a conformidade com as normas e para facilitar futuras manutenções.
6. Não Realizar Testes de Funcionamento
Após a calibração, é crucial realizar testes de funcionamento para garantir que a válvula opere corretamente. Ignorar essa etapa pode resultar em falhas que não foram detectadas durante a calibração. Para evitar esse erro, sempre teste a válvula após a calibração, monitorando a pressão e verificando se a válvula abre e fecha conforme esperado. Isso ajudará a identificar quaisquer problemas antes que a válvula seja colocada de volta em operação.
7. Falta de Treinamento Adequado
Um erro comum que pode comprometer a calibração de válvulas de segurança é a falta de treinamento adequado dos profissionais responsáveis pelo procedimento. A calibração requer conhecimento técnico e habilidades específicas, e a falta de treinamento pode levar a erros graves. Para evitar esse problema, invista em treinamentos regulares para sua equipe, garantindo que todos os envolvidos no processo de calibração estejam atualizados sobre as melhores práticas e as normas de segurança.
8. Ignorar a Manutenção Regular
A calibração de válvulas de segurança deve ser parte de um programa abrangente de manutenção preventiva. Ignorar a manutenção regular pode levar a problemas que afetam a calibração e o desempenho da válvula. Para evitar esse erro, estabeleça um cronograma de manutenção que inclua inspeções e calibrações periódicas. Isso garantirá que as válvulas permaneçam em boas condições de funcionamento e que atendam às normas de segurança.
Em resumo, a calibração de válvulas de segurança é um processo crítico que deve ser realizado com atenção e cuidado. Evitar os erros comuns discutidos acima pode ajudar a garantir que as válvulas funcionem corretamente, contribuindo para a segurança operacional e a eficiência dos sistemas industriais. A implementação de boas práticas, como planejamento adequado, inspeções visuais, uso de equipamentos calibrados e documentação detalhada, é fundamental para o sucesso da calibração e para a proteção de todos os envolvidos nas operações industriais.
Manutenção e Verificação Regular da Válvula de Segurança após a Calibração
A manutenção e verificação regular das válvulas de segurança são essenciais para garantir que esses dispositivos funcionem corretamente e cumpram sua função de proteção em sistemas industriais. Após a calibração, é fundamental estabelecer um cronograma de manutenção que inclua inspeções periódicas e testes de funcionamento. A seguir, discutiremos a importância da manutenção, as práticas recomendadas e como realizar verificações regulares nas válvulas de segurança.
1. Importância da Manutenção Regular
A manutenção regular das válvulas de segurança é crucial para garantir a segurança operacional e a eficiência dos sistemas. Com o tempo, as válvulas podem sofrer desgaste devido a fatores como pressão, temperatura e corrosão. Se não forem mantidas adequadamente, podem falhar em momentos críticos, resultando em acidentes graves, danos materiais e até mesmo riscos à vida. Portanto, a manutenção regular é uma prática preventiva que ajuda a identificar e corrigir problemas antes que se tornem críticos.
2. Estabelecendo um Cronograma de Manutenção
Um cronograma de manutenção deve ser estabelecido com base nas recomendações do fabricante, nas normas de segurança aplicáveis e nas condições operacionais específicas. É importante considerar fatores como a frequência de uso da válvula, o ambiente em que está instalada e as características do fluido que passa por ela. Um cronograma típico pode incluir inspeções mensais, testes semestrais e calibrações anuais, mas esses intervalos podem variar conforme a necessidade.
3. Inspeções Visuais
As inspeções visuais são uma parte fundamental da manutenção regular. Durante essas inspeções, os profissionais devem verificar se há sinais de desgaste, corrosão, vazamentos ou danos visíveis nas válvulas e em suas conexões. Qualquer anomalia deve ser documentada e corrigida imediatamente. Além disso, é importante verificar se as etiquetas de identificação e as informações de calibração estão legíveis e atualizadas.
4. Testes de Funcionamento
Após a calibração, é essencial realizar testes de funcionamento regulares para garantir que a válvula opere corretamente. Esses testes devem incluir a verificação da pressão de abertura e fechamento, bem como a resposta da válvula a variações de pressão. Os testes devem ser realizados em condições operacionais reais, sempre que possível, para garantir que a válvula funcione conforme esperado. Caso a válvula não responda adequadamente, ajustes ou reparos devem ser realizados imediatamente.
5. Uso de Tecnologias Avançadas
Para otimizar a manutenção e verificação das válvulas de segurança, muitas indústrias estão adotando tecnologias avançadas, como o Ensaio não destrutivo ultrassom. Essa técnica permite a detecção de falhas internas e a avaliação da integridade das válvulas sem a necessidade de desmontá-las. O uso de ensaios não destrutivos pode economizar tempo e recursos, além de proporcionar uma análise mais precisa do estado das válvulas.
6. Lubrificação e Ajustes
A lubrificação adequada das partes móveis das válvulas de segurança é essencial para garantir seu funcionamento suave e eficiente. Durante as inspeções regulares, os profissionais devem verificar se as áreas de lubrificação estão limpas e se o lubrificante está em boas condições. Se necessário, aplique um lubrificante apropriado conforme as recomendações do fabricante. Além disso, ajustes nas configurações da válvula podem ser necessários ao longo do tempo, especialmente se houver mudanças nas condições operacionais.
7. Documentação e Registro
Manter registros detalhados de todas as atividades de manutenção e verificação é fundamental para garantir a conformidade com as normas de segurança e facilitar auditorias futuras. Os registros devem incluir datas de inspeção, resultados dos testes, ajustes realizados e quaisquer observações relevantes. Essa documentação não apenas ajuda a manter a rastreabilidade, mas também pode ser útil para identificar tendências de desgaste e planejar manutenções futuras.
8. Treinamento da Equipe
Para garantir a eficácia da manutenção e verificação das válvulas de segurança, é essencial que a equipe responsável esteja devidamente treinada. O treinamento deve incluir informações sobre as melhores práticas de manutenção, procedimentos de inspeção e testes, bem como o uso de tecnologias avançadas. Investir no treinamento da equipe ajuda a minimizar erros e a garantir que as válvulas sejam mantidas em conformidade com as normas de segurança.
9. Revisão e Atualização do Cronograma
O cronograma de manutenção deve ser revisado e atualizado regularmente com base nas condições operacionais e nos resultados das inspeções. Se forem identificados problemas recorrentes ou se as condições de operação mudarem, o cronograma deve ser ajustado para garantir que as válvulas de segurança permaneçam em boas condições de funcionamento. Essa abordagem proativa ajuda a evitar falhas e a garantir a segurança operacional.
Em resumo, a manutenção e verificação regular das válvulas de segurança após a calibração são essenciais para garantir a segurança e a eficiência dos sistemas industriais. Estabelecer um cronograma de manutenção, realizar inspeções visuais, testes de funcionamento e utilizar tecnologias avançadas são práticas fundamentais para garantir que as válvulas operem corretamente. Além disso, a documentação adequada e o treinamento da equipe são cruciais para manter a conformidade com as normas de segurança e garantir a proteção de todos os envolvidos nas operações industriais.
Em conclusão, a calibração de válvulas de segurança é um elemento vital para a operação segura e eficiente de sistemas industriais. Através de um processo metódico que inclui planejamento, inspeção, testes e manutenção regular, é possível garantir que essas válvulas funcionem de maneira eficaz, prevenindo falhas que podem levar a acidentes e danos significativos. Ao evitar erros comuns e implementar práticas de manutenção adequadas, as indústrias podem não apenas cumprir as normas de segurança, mas também proteger seus colaboradores e ativos. Portanto, investir tempo e recursos na calibração e manutenção das válvulas de segurança é uma decisão inteligente que resulta em operações mais seguras e sustentáveis.