Calibração de Válvula de Segurança: Manutenção Essencial para sua Operação
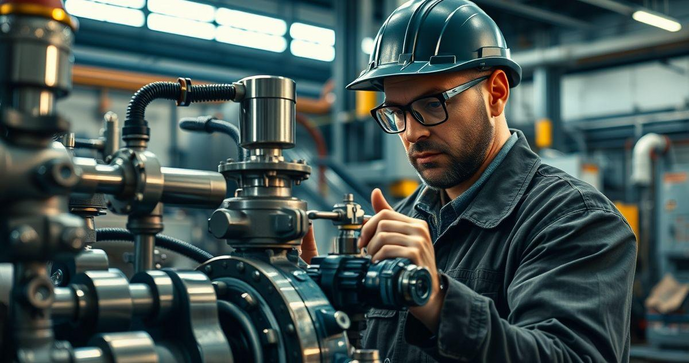
Por: Walter - 28 de Fevereiro de 2025
A calibração da válvula de segurança é um procedimento crucial para garantir a operação eficiente e segura de sistemas industriais e de aquecimento. Este processo assegura que a válvula funcione corretamente, evitando riscos de sobrepressão e possíveis acidentes. Neste artigo, abordaremos a importância da calibração, o passo a passo para realizá-la, além de dicas para evitar erros comuns e garantir a manutenção adequada desse componente vital.
Importância da Calibração da Válvula de Segurança
A calibração da válvula de segurança é um aspecto fundamental na operação de sistemas que lidam com pressão, como caldeiras, compressores e tubulações industriais. Essas válvulas desempenham um papel crucial na proteção de equipamentos e na segurança dos trabalhadores, evitando situações de sobrepressão que podem resultar em falhas catastróficas. Portanto, entender a importância da calibração é essencial para garantir a integridade do sistema e a segurança operacional.
Uma válvula de segurança calibrada corretamente assegura que a pressão interna de um sistema não ultrapasse os limites seguros. Quando a pressão atinge um nível crítico, a válvula deve abrir automaticamente para liberar o excesso de pressão, evitando danos ao equipamento e prevenindo acidentes. Se a válvula não estiver calibrada adequadamente, pode não abrir na pressão correta, resultando em riscos significativos, como explosões ou vazamentos perigosos.
Além da segurança, a calibração da válvula de segurança também impacta a eficiência operacional. Válvulas que não funcionam corretamente podem levar a perdas de energia e aumento de custos operacionais. Por exemplo, se uma válvula de segurança abrir em uma pressão mais baixa do que o necessário, o sistema pode operar de forma ineficiente, resultando em ciclos de operação desnecessários e desperdício de recursos. Portanto, a calibração não é apenas uma questão de segurança, mas também de eficiência econômica.
Outro ponto a ser considerado é a conformidade com normas e regulamentos. Muitas indústrias são obrigadas a seguir diretrizes específicas de segurança e manutenção, que incluem a calibração regular das válvulas de segurança. A não conformidade pode resultar em penalidades legais, além de comprometer a segurança dos trabalhadores e a integridade do ambiente de trabalho. Portanto, manter a calibração em dia é uma responsabilidade legal e ética para as empresas.
Além disso, a calibração da válvula de segurança deve ser realizada por profissionais qualificados, utilizando equipamentos adequados. O uso de tecnologias como o Ultrassom industrial pode ser uma solução eficaz para verificar a integridade e o funcionamento das válvulas. Essa tecnologia permite detectar vazamentos e falhas que podem não ser visíveis a olho nu, garantindo que a válvula esteja operando dentro dos parâmetros estabelecidos.
É importante ressaltar que a calibração não deve ser vista como uma tarefa única, mas sim como parte de um programa contínuo de manutenção. As condições de operação, como temperatura, pressão e ambiente, podem afetar o desempenho da válvula ao longo do tempo. Portanto, realizar calibrações regulares e inspeções periódicas é essencial para garantir que a válvula de segurança continue a funcionar corretamente.
Além disso, a calibração deve ser documentada adequadamente. Manter registros detalhados das calibrações realizadas, incluindo datas, resultados e quaisquer ajustes feitos, é fundamental para a gestão de manutenção. Esses registros não apenas ajudam a monitorar o desempenho da válvula ao longo do tempo, mas também são essenciais para auditorias e inspeções regulatórias.
Por fim, a conscientização sobre a importância da calibração da válvula de segurança deve ser disseminada entre todos os colaboradores da empresa. Treinamentos regulares e workshops podem ajudar a garantir que todos entendam a função crítica das válvulas de segurança e a necessidade de mantê-las calibradas. Uma cultura de segurança forte dentro da organização pode prevenir acidentes e promover um ambiente de trabalho mais seguro.
Em resumo, a calibração da válvula de segurança é um componente vital para a segurança e eficiência de sistemas industriais. Através da calibração adequada, é possível garantir que as válvulas funcionem corretamente, evitando riscos de sobrepressão e promovendo a conformidade com normas de segurança. Investir em calibração regular e em tecnologias avançadas, como o Ultrassom industrial, é uma estratégia inteligente para proteger tanto os equipamentos quanto os trabalhadores, assegurando um ambiente de trabalho seguro e eficiente.
Passo a Passo para Realizar a Calibração
Realizar a calibração da válvula de segurança é um procedimento essencial para garantir a segurança e a eficiência de sistemas que operam sob pressão. A calibração deve ser feita de forma metódica e cuidadosa, seguindo um conjunto de etapas que asseguram que a válvula funcione corretamente. Abaixo, apresentamos um passo a passo detalhado para realizar a calibração da válvula de segurança.
1. Preparação e Planejamento
Antes de iniciar o processo de calibração, é fundamental realizar um planejamento adequado. Isso inclui a coleta de informações sobre a válvula a ser calibrada, como seu modelo, especificações técnicas e pressão de abertura. Além disso, é importante verificar se todos os equipamentos necessários para a calibração estão disponíveis e em boas condições de funcionamento. Isso pode incluir manômetros, chaves de fenda, ferramentas de ajuste e, se necessário, dispositivos de medição eletrônicos.
2. Desligamento do Sistema
Antes de realizar qualquer trabalho na válvula de segurança, é crucial desligar o sistema em que ela está instalada. Isso garante a segurança do operador e evita acidentes. Após o desligamento, é importante liberar a pressão do sistema para garantir que não haja risco de vazamentos ou explosões durante o processo de calibração. Certifique-se de seguir os procedimentos de segurança estabelecidos pela empresa e pelas normas regulatórias, como as Inspeções nr13.
3. Remoção da Válvula
Com o sistema desligado e a pressão liberada, o próximo passo é remover a válvula de segurança do sistema. Isso pode envolver a desconexão de tubulações e a remoção de parafusos ou suportes que prendem a válvula ao equipamento. É importante manusear a válvula com cuidado para evitar danos. Após a remoção, inspecione a válvula em busca de sinais de desgaste ou danos que possam afetar seu desempenho.
4. Calibração da Válvula
Com a válvula removida, é hora de realizar a calibração. Para isso, conecte a válvula a um manômetro calibrado que permita medir a pressão de abertura. Gradualmente, aumente a pressão do sistema até atingir o ponto de abertura especificado para a válvula. Observe a pressão no manômetro e verifique se a válvula abre no ponto correto. Se a válvula abrir antes ou depois da pressão especificada, será necessário realizar ajustes.
Os ajustes podem ser feitos através de um parafuso de ajuste localizado na parte superior da válvula. Gire o parafuso no sentido horário para aumentar a pressão de abertura e no sentido anti-horário para diminuí-la. Após cada ajuste, repita o teste de pressão para verificar se a válvula agora abre na pressão correta. Esse processo pode exigir várias tentativas até que a calibração esteja correta.
5. Teste de Funcionamento
Após a calibração, é importante realizar um teste de funcionamento da válvula. Isso envolve simular uma situação de sobrepressão para garantir que a válvula abra e feche corretamente. Aumente a pressão gradualmente até que a válvula atinja o ponto de abertura e observe se ela se fecha adequadamente quando a pressão é reduzida. Esse teste é crucial para garantir que a válvula funcione conforme o esperado em situações reais.
6. Reinstalação da Válvula
Com a calibração e os testes concluídos, a válvula pode ser reinstalada no sistema. Certifique-se de que todas as conexões estejam firmes e que não haja vazamentos. Reinstale a válvula seguindo as instruções do fabricante e assegure-se de que todos os suportes e parafusos estejam bem apertados. Após a reinstalação, é importante realizar uma verificação final para garantir que tudo esteja em ordem.
7. Documentação e Registro
Por fim, é essencial documentar todo o processo de calibração. Registre a data da calibração, os resultados dos testes, quaisquer ajustes realizados e a pressão de abertura final. Manter um registro detalhado é importante para auditorias futuras e para garantir a conformidade com as normas de segurança. Além disso, esses registros podem ser úteis para futuras manutenções e calibrações.
Realizar a calibração da válvula de segurança é um procedimento que exige atenção e cuidado. Seguir este passo a passo não apenas garante a segurança do sistema, mas também contribui para a eficiência operacional. A calibração regular e a documentação adequada são práticas recomendadas que ajudam a manter a integridade do sistema e a segurança dos trabalhadores.
Erros Comuns na Calibração e Como Evitá-los
A calibração da válvula de segurança é um processo crítico que garante a segurança e a eficiência de sistemas que operam sob pressão. No entanto, existem erros comuns que podem ocorrer durante esse processo, comprometendo a eficácia da válvula e colocando em risco a segurança do sistema. Neste artigo, abordaremos os principais erros na calibração e como evitá-los, assegurando que a válvula funcione corretamente e de forma segura.
1. Falta de Planejamento Adequado
Um dos erros mais frequentes na calibração da válvula de segurança é a falta de planejamento. Muitas vezes, os profissionais iniciam o processo sem uma compreensão clara das especificações da válvula, dos equipamentos necessários e dos procedimentos a serem seguidos. Para evitar esse erro, é fundamental realizar um planejamento detalhado antes de iniciar a calibração. Isso inclui a coleta de informações sobre a válvula, como seu modelo, pressão de abertura e requisitos de manutenção. Além disso, é importante garantir que todas as ferramentas e equipamentos, como manômetros e dispositivos de medição, estejam disponíveis e em boas condições.
2. Ignorar a Liberação de Pressão
Outro erro comum é não liberar a pressão do sistema antes de iniciar a calibração. Trabalhar em uma válvula sob pressão pode resultar em acidentes graves, como vazamentos ou explosões. Para evitar esse risco, sempre siga os procedimentos de segurança estabelecidos pela empresa e pelas normas regulatórias. Certifique-se de que a pressão do sistema esteja completamente liberada antes de remover a válvula ou iniciar o processo de calibração. Isso não apenas protege os operadores, mas também garante que a calibração seja realizada em condições seguras.
3. Não Realizar Testes de Funcionamento
Após a calibração, é essencial realizar testes de funcionamento para garantir que a válvula opere corretamente. Um erro comum é pular essa etapa, acreditando que a calibração foi suficiente. Para evitar isso, sempre simule uma situação de sobrepressão após a calibração e verifique se a válvula abre e fecha conforme esperado. Realizar testes de funcionamento ajuda a identificar problemas que podem não ser visíveis durante a calibração e assegura que a válvula esteja pronta para operar em condições reais.
4. Ajustes Inadequados
Durante a calibração, pode haver a tentação de fazer ajustes inadequados na válvula, como aumentar ou diminuir a pressão de abertura sem seguir as especificações do fabricante. Isso pode resultar em uma válvula que não funciona corretamente, abrindo em pressões inadequadas. Para evitar esse erro, sempre consulte o manual do fabricante e siga as diretrizes específicas para ajustes. Utilize manômetros calibrados e confiáveis para garantir que a pressão de abertura esteja dentro dos parâmetros corretos.
5. Falta de Documentação
A documentação é uma parte crucial do processo de calibração, mas muitas vezes é negligenciada. Não manter registros detalhados das calibrações realizadas, incluindo datas, resultados e ajustes, pode levar a problemas futuros. Para evitar esse erro, crie um sistema de documentação que registre todas as calibrações e manutenções realizadas. Isso não apenas ajuda na conformidade com as normas de segurança, mas também fornece um histórico útil para futuras manutenções e calibrações. Além disso, considere a Calibração de manometros como parte do processo, garantindo que todos os instrumentos utilizados estejam precisos.
6. Não Treinar a Equipe Adequadamente
A falta de treinamento adequado para a equipe responsável pela calibração é um erro que pode ter consequências graves. Profissionais não treinados podem cometer erros durante o processo, comprometendo a segurança do sistema. Para evitar esse problema, invista em treinamentos regulares e workshops para a equipe. Certifique-se de que todos os envolvidos no processo de calibração compreendam a importância da tarefa e estejam familiarizados com os procedimentos corretos. Uma equipe bem treinada é fundamental para garantir a eficácia da calibração e a segurança do sistema.
7. Ignorar as Condições Ambientais
As condições ambientais, como temperatura e umidade, podem afetar o desempenho da válvula de segurança. Ignorar esses fatores durante a calibração pode resultar em medições imprecisas e funcionamento inadequado da válvula. Para evitar esse erro, sempre considere as condições ambientais ao realizar a calibração. Se necessário, ajuste os procedimentos de calibração para levar em conta as variações nas condições ambientais, garantindo que a válvula funcione corretamente em todas as situações.
Em resumo, a calibração da válvula de segurança é um processo crítico que deve ser realizado com atenção e cuidado. Evitar erros comuns, como falta de planejamento, não liberar a pressão, pular testes de funcionamento, fazer ajustes inadequados, não documentar, não treinar a equipe e ignorar as condições ambientais, é essencial para garantir a segurança e a eficiência do sistema. Ao seguir as melhores práticas e estar ciente dos erros potenciais, você pode assegurar que a válvula de segurança funcione corretamente e proteja tanto os equipamentos quanto os trabalhadores.
Manutenção e Verificação Regular da Válvula de Segurança
A manutenção e verificação regular da válvula de segurança são essenciais para garantir a segurança e a eficiência de sistemas que operam sob pressão. Essas válvulas desempenham um papel crucial na proteção de equipamentos e na prevenção de acidentes, liberando pressão excessiva quando necessário. Portanto, é fundamental estabelecer um programa de manutenção que inclua inspeções regulares, testes e reparos, assegurando que a válvula funcione corretamente em todas as situações.
1. Importância da Manutenção Regular
A manutenção regular da válvula de segurança é vital para evitar falhas que podem resultar em acidentes graves. Com o tempo, as válvulas podem sofrer desgaste devido a fatores como corrosão, acúmulo de sujeira e variações de temperatura. Esses fatores podem comprometer o funcionamento da válvula, fazendo com que ela não abra ou feche corretamente. A manutenção preventiva ajuda a identificar e corrigir problemas antes que eles se tornem críticos, garantindo a segurança do sistema e a integridade dos equipamentos.
2. Inspeções Visuais
Uma das primeiras etapas na manutenção da válvula de segurança é realizar inspeções visuais regulares. Isso envolve verificar se há sinais de desgaste, corrosão ou danos visíveis na válvula e em suas conexões. Durante a inspeção, é importante observar se há vazamentos, que podem indicar problemas na vedação da válvula. Se forem identificados problemas durante a inspeção visual, é fundamental tomar medidas corretivas imediatamente, como reparos ou substituições, para evitar falhas no sistema.
3. Testes de Funcionamento
Além das inspeções visuais, é essencial realizar testes de funcionamento regulares na válvula de segurança. Esses testes devem simular condições de operação reais, aumentando gradualmente a pressão até que a válvula abra. É importante monitorar a pressão em que a válvula se abre e se fecha, garantindo que esses valores estejam dentro das especificações do fabricante. Se a válvula não abrir na pressão correta, ajustes devem ser feitos imediatamente para garantir seu funcionamento adequado.
4. Registro de Manutenção
Manter registros detalhados de todas as atividades de manutenção e verificação é uma prática recomendada que não deve ser negligenciada. Esses registros devem incluir datas de inspeção, resultados de testes, ajustes realizados e quaisquer reparos feitos. A documentação adequada é fundamental para auditorias e para garantir a conformidade com as normas de segurança. Além disso, esses registros ajudam a identificar padrões de desgaste e a programar manutenções futuras de forma mais eficaz.
5. Ensaio Não Destrutivo
Uma técnica eficaz para garantir a integridade da válvula de segurança é o Ensaio não destrutivo ultrassom. Essa técnica permite detectar falhas internas e desgastes que não são visíveis a olho nu, garantindo que a válvula esteja em condições adequadas de operação. O ensaio não destrutivo é uma ferramenta valiosa para a manutenção preventiva, pois ajuda a identificar problemas antes que eles se tornem críticos, aumentando a segurança do sistema.
6. Treinamento da Equipe
Para garantir a eficácia da manutenção e verificação da válvula de segurança, é fundamental que a equipe responsável esteja bem treinada. O treinamento deve incluir informações sobre os procedimentos de manutenção, a importância da verificação regular e como identificar sinais de desgaste ou falhas. Uma equipe bem treinada é capaz de realizar manutenções de forma eficaz e identificar problemas antes que eles se tornem críticos, contribuindo para a segurança do sistema.
7. Frequência das Manutenções
A frequência das manutenções e verificações deve ser determinada com base nas recomendações do fabricante, nas condições de operação e nas normas regulatórias. Em geral, é recomendável realizar inspeções visuais e testes de funcionamento pelo menos uma vez por ano. No entanto, em sistemas que operam em condições severas ou que apresentam alta frequência de uso, pode ser necessário aumentar a frequência das manutenções. Avaliar regularmente as condições de operação e ajustar o cronograma de manutenção conforme necessário é fundamental para garantir a segurança e a eficiência do sistema.
8. Substituição de Componentes
Durante as inspeções e manutenções, pode ser necessário substituir componentes da válvula de segurança, como vedantes, molas ou outros elementos que apresentem desgaste. A substituição de componentes desgastados é essencial para garantir que a válvula funcione corretamente e mantenha sua capacidade de liberar pressão excessiva. Sempre utilize peças de reposição recomendadas pelo fabricante para garantir a compatibilidade e a eficácia da válvula.
Em resumo, a manutenção e verificação regular da válvula de segurança são essenciais para garantir a segurança e a eficiência de sistemas que operam sob pressão. Através de inspeções visuais, testes de funcionamento, documentação adequada e o uso de técnicas como o ensaio não destrutivo, é possível identificar e corrigir problemas antes que eles se tornem críticos. Investir em treinamento da equipe e estabelecer um cronograma de manutenção adequado são práticas recomendadas que contribuem para a segurança e a integridade do sistema. Ao seguir essas diretrizes, você pode assegurar que a válvula de segurança funcione corretamente e proteja tanto os equipamentos quanto os trabalhadores.
A calibração da válvula de segurança é um procedimento essencial que não deve ser negligenciado em sistemas industriais e de aquecimento. Através de uma calibração adequada, é possível garantir que a válvula opere de forma eficiente, prevenindo riscos de sobrepressão e assegurando a segurança dos equipamentos e das pessoas envolvidas. Ao seguir o passo a passo apresentado, realizar manutenções regulares e evitar erros comuns, você estará contribuindo para a integridade do sistema e a proteção do ambiente de trabalho. Investir tempo e recursos na calibração e manutenção da válvula de segurança é um compromisso com a segurança e a eficiência operacional, que traz benefícios a longo prazo para sua empresa.