Guia Completo sobre Calibração de Manômetros para Precisão em Medidas
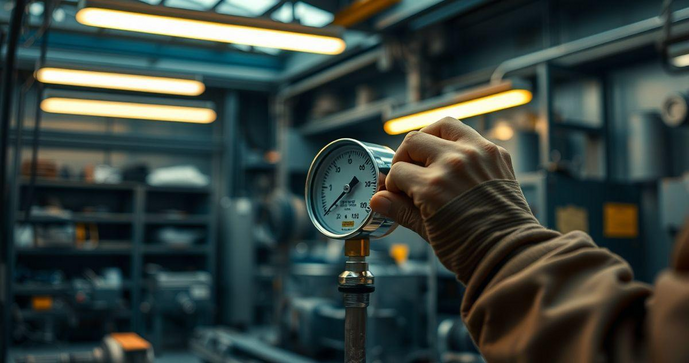
Por: Walter - 25 de Março de 2025
Importância da Calibração de Manômetros na Indústria
A calibração de manômetros é fundamental na indústria, pois assegura que as medições de pressão sejam precisas e confiáveis.
Em setores como o petroquímico, farmacêutico e alimentício, por exemplo, a precisão na medição da pressão pode impactar diretamente a qualidade do produto final e a segurança operacional.
1. Garantia da Qualidade: A calibração regular dos manômetros garante que as medições estejam dentro das especificações requeridas, evitando desvios que possam levar à produção de produtos defeituosos.
Isso é especialmente crítico em indústrias onde a qualidade é monitorada rigorosamente, como na farmacêutica, onde até pequenas variações podem comprometer a eficácia de um medicamento.
2. Segurança Operacional: Manômetros calibrados corretamente são essenciais para a segurança em processos industriais.
Pressões inadequadas podem levar a explosões, vazamentos ou falhas em equipamentos, representando riscos tanto para os trabalhadores quanto para o meio ambiente.
A calibração ajuda a garantir que os sistemas estejam operando dentro de parâmetros seguros.
3. Conformidade Normativa: Muitas indústrias são regulamentadas por normas que exigem a calibração regular dos instrumentos de medição.
A conformidade com essas normas é necessária não apenas para atender a requisitos legais, mas também para evitar multas e prejuízos à reputação da empresa.
4. Eficiência Operacional: A calibração de manômetros pode levar a uma operação mais eficiente dos sistemas industriais.
Medições precisas permitem ajustes finos nos processos, resultando em maior eficiência energética e redução de desperdícios, o que é crucial em um cenário de aumento de custos.
5. Redução de Custos: Investir na calibração de manômetros pode parecer um custo adicional, mas, a longo prazo, pode ajudar a reduzir despesas operacionais.
Sistemas que operam com manômetros não calibrados tendem a enfrentar mais problemas e paradas, resultando em custos elevados com manutenção e reparos.
A calibração preventiva mantém a saúde do equipamento e prolonga sua vida útil.
Portanto, a calibração de manômetros não deve ser vista apenas como uma tarefa técnica, mas como uma prática vital para garantir a qualidade, segurança e eficiência das operações industriais.
Como Funciona o Processo de Calibração de Manômetros
O processo de calibração de manômetros envolve uma série de etapas que garantem medições de pressão precisas e confiáveis.
A seguir, descreveremos o funcionamento desse processo de forma detalhada.
1. Preparação e Verificação Inicial: Antes de iniciar a calibração, o manômetro deve ser verificado quanto a danos físicos ou a sujeira acumulada, que podem interferir na precisão das medições.
Caso o manômetro apresente qualquer tipo de anomalia, este deve ser reparado ou substituído antes da calibração.
2. Equipamento de Calibração: Para a calibração, utiliza-se um padrão de referência, que pode ser um manômetro de alta precisão ou um calibrador de pressão.
Esse equipamento é essencial, pois serve como base para comparar e ajustar o manômetro que está sendo calibrado.
3. Criação de Ponto de Referência: O primeiro passo no processo de calibração é conectar o manômetro a ser calibrado ao equipamento de referência.
Em seguida, é importante estabelecer pontos de referência, que normalmente são definidos por um conjunto de pressões específicas ao longo da faixa de operação do manômetro.
4. Aplicação de Pressão: A pressão é gradualmente aplicada ao manômetro em cada um dos pontos de referência.
Durante essa etapa, as leituras do manômetro a ser calibrado são registradas e comparadas às leituras do equipamento de alta precisão.
Essa comparação ajuda a identificar o desvio em relação ao padrão de referência.
5. Ajustes e Correções: Se o manômetro apresentar desvios em relação ao padrão durante a comparação, ajustes devem ser feitos.
Dependendo do tipo de manômetro, isso pode envolver a calibração mecânica ou elétrica, através de um parafuso de ajuste ou pelo software do instrumento.
O objetivo é alinhar a leitura do manômetro com os valores reais de pressão.
6. Verificação de Desempenho: Após os ajustes, o manômetro deve ser testado novamente em todos os pontos de referência para garantir que agora as leituras estão corretas.
Essa verificação é crucial para assegurar que o manômetro poderá ser utilizado com confiança nas medições.
7. Documentação: Por fim, é importante registrar todos os dados da calibração, incluindo os pontos de referência, os valores observados e quaisquer ajustes realizados.
Essa documentação é essencial para garantir a rastreabilidade e pode ser necessária para atender requisitos regulatórios.
Em resumo, a calibração de manômetros é um processo metódico que envolve preparação, medição, ajustes e documentação, assegurando que os instrumentos de medição operem com precisão e confiabilidade em ambientes industriais.
Tipos de Manômetros e Suas Necessidades de Calibração
Existem diversos tipos de manômetros utilizados na indústria, cada um com suas características específicas e necessidades de calibração. A seguir, apresentamos os principais tipos de manômetros e as particularidades de calibração associadas a cada um deles.
1. Manômetros Mecânicos: Esses manômetros utilizam componentes mecânicos, como tubos de Bourdon ou membranas, para medir a pressão. São amplamente usados devido à sua simplicidade e confiabilidade. A calibração deve ocorrer regularmente, especialmente após longos períodos de uso, já que a deformação dos componentes pode afetar a precisão. Normalmente, recomenda-se a calibração a cada 6 meses ou anualmente.
2. Manômetros Digitais: Os manômetros digitais utilizam sensores eletrônicos para medir a pressão e oferecem uma leitura de resultado no formato digital. Embora sejam mais precisos que os mecânicos, sua calibração pode ser mais complexa e muitas vezes depende de software. A necessidade de calibração pode variar de acordo com o fabricante, mas geralmente é aconselhável realizar a calibração anualmente.
3. Manômetros de Alta Pressão: Utilizados em processos que lidam com pressões elevadas, esses manômetros devem ser calibrados com frequência devido às condições severas em que operam. A calibração deve ser feita utilizando equipamento especializado que suporte as altas pressões para garantir precisão nas medições. Recomenda-se uma verificação a cada 3 a 6 meses.
4. Manômetros de Vácuo: Esses instrumentos medem pressões abaixo da atmosférica. A calibração é essencial para assegurar a precisão, especialmente em aplicações químicas ou farmacêuticas. A calibração deve ocorrer regularmente, dependendo do uso, mas em média, a cada 6 meses é uma prática recomendada.
5. Manômetros de Diferencial: Esses manômetros medem a diferença de pressão entre dois pontos. A calibração é crucial para garantir a precisão nas medições de fluxo ou pressão em sistemas complexos. Este tipo de manômetro deve ser calibrado periodicamente, de acordo com as especificações do fabricante, mas em geral, a cada 6 meses é uma boa prática.
6. Manômetros de Pressão Absoluta: Utilizados para medir pressão em relação ao vácuo perfeito. A calibração deve ser realizada com um padrão de referência absoluto para garantir a exatidão. Devido à sensibilidade desses instrumentos, recomenda-se uma calibração anual, ou mais frequente em ambientes onde a precisão é crítica.
Em resumo, a escolha do tipo de manômetro a ser utilizado impacta diretamente nas necessidades de calibração. É fundamental seguir as recomendações dos fabricantes e realizar calibrações regulares, garantindo a precisão e confiabilidade das medições nos processos industriais.
Fatores que Afetam a Precisão dos Manômetros
A precisão dos manômetros é crucial para garantir medições de pressão confiáveis em diversos setores da indústria. No entanto, vários fatores podem influenciar essa precisão. A seguir, exploramos os principais fatores que afetam a exatidão dos manômetros.
1. Temperatura: A temperatura do ambiente onde o manômetro está instalado pode ter um grande impacto na precisão da leitura. Mudanças significativas na temperatura podem causar dilatação nos componentes do manômetro, resultando em leituras imprecisas. Portanto, é importante calibrar o manômetro em condições de temperatura semelhantes às condições de operação.
2. Umidade: A umidade também pode afetar a precisão dos manômetros, especialmente os mecânicos. A presença de umidade pode causar corrosão em componentes internos e interferir nas medições. Para manômetros digitais, a umidade pode danificar os circuitos eletrônicos, levando a falhas nas leituras. A resistência à umidade e a instalação em ambientes controlados são considerações importantes.
3. Vibrações: Em ambientes industriais, vibrações constantes podem afetar a estabilidade dos manômetros, especialmente os mecânicos. Vibrações podem causar desvio nas leituras e, em alguns casos, danificar os componentes internos. O uso de suportes adequados e a instalação em locais menos sujeitos à vibração podem ajudar a minimizar esse impacto.
4. Pressão de Referência: Manômetros que medem a pressão relativa são afetados pela pressão atmosférica, já que suas leituras dependem da pressão de referência. Se a pressão de referência não for constante ou precisa, as medições também serão afetadas. É crucial verificar regularmente a precisão da pressão de referência para garantir medições corretas.
5. Condições de Instalação: A forma como um manômetro é instalado pode impactar sua precisão. Instalações incorretas, como posicionamento inadequado ou conexões inadequadas, podem levar a medições errôneas. O alinhamento correto e o uso de conexões apropriadas são fundamentais para manter a precisão do instrumento.
6. Usura e Dano: Com o tempo, os componentes dos manômetros podem sofrer desgaste ou dano, o que pode afetar sua precisão. Elementos como tubos de Bourdon ou membranas podem se deformar e perder a capacidade de fornecer leituras exatas. Realizar manutenção regular e calibrações frequentes é essencial para identificar e corrigir problemas de desgaste.
7. Qualidade do Instrumento: A precisão dos manômetros também está relacionada à sua qualidade de fabricação. Manômetros de baixa qualidade podem não oferecer a confiabilidade necessária, resultando em medições imprecisas. Investir em instrumentos de qualidade e conhecidos no mercado é crucial para minimizar erros nas medições.
Em resumo, diversos fatores podem influenciar a precisão dos manômetros. A compreensão desses fatores e a implementação de práticas de manutenção adequadas são essenciais para garantir medições de pressão confiáveis e eficazes em ambientes industriais.
Dicas para Manutenção e Calibração Eficiente
A manutenção e a calibração eficientes de manômetros são essenciais para garantir medições precisas e prolongar a vida útil dos instrumentos. A seguir, apresentamos algumas dicas práticas que podem auxiliar na implementação de um programa eficaz de manutenção e calibração.
1. Estabeleça um Cronograma Regular: Criar um cronograma de calibração e manutenção regular é fundamental. Dependendo do tipo de manômetro e do ambiente em que está instalado, defina intervalos de verificação, que podem variar de mensal a anual. Documente todos os testes e calibrações realizados para acompanhar a condição do manômetro ao longo do tempo.
2. Use Equipamentos de Referência de Alta Precisão: Para a calibração, sempre utilize equipamentos de referência certificados e calibrados. Isso garante que o manômetro em teste seja comparado a um padrão confiável, minimizando erros nas medições. Verifique se o equipamento de referência está dentro do período de validade de calibração.
3. Treinamento da Equipe: Conduza treinamentos regulares para a equipe responsável pela calibração e manutenção dos manômetros. Uma equipe bem-informada terá maior conhecimento sobre os processos e práticas corretas, o que facilitará a identificação de problemas antes que se tornem críticos.
4. Condições de Armazenamento Adequadas: Os manômetros devem ser armazenados em condições que minimizem o risco de danos. Evite expô-los a temperaturas extremas, umidade excessiva ou vibrações. O uso de proteções e embalagens adequadas pode ajudar a preservar a integridade dos instrumentos durante o transporte ou armazenamento.
5. Limpeza Regular: Mantenha os manômetros limpos e livres de sujeira e contaminantes. Realize limpezas visuais regulares, removendo qualquer resíduo que possa obstruir a operação. Use produtos de limpeza adequados que não danifiquem os componentes do manômetro.
6. Verificação de Conexões: Inspecione periodicamente todas as conexões e tubulações associadas aos manômetros. Conexões soltas ou desgastadas podem levar a vazamentos e leituras imprecisas. Assegure que todas as conexões estejam firmes e em boas condições.
7. Documentação e Rastreabilidade: Mantenha registros detalhados de todas as calibrações e manutenções realizadas. Isso não apenas ajuda na rastreabilidade, mas também permite que a equipe identifique padrões de desgaste ou falhas ao longo do tempo. A documentação adequada é especialmente importante para atender a requisitos regulatórios.
8. Respostas Rápidas a Problemas: Esteja preparado para agir rapidamente caso se identifiquem problemas nos manômetros. Se uma leitura parecer inconsistente, realize uma verificação de precisão imediatamente. A correção rápida de problemas pode evitar prejuízos significativos em processos industriais.
Adotar essas práticas pode garantir a eficácia da manutenção e calibração de manômetros, resultando em medições confiáveis e aumento da segurança operacional. A atenção contínua à manutenção preventiva ajudará a evitar falhas e garantirá a funcionalidade dos manômetros ao longo do tempo.
Quando Realizar a Calibração de Manômetros
Realizar a calibração de manômetros em intervalos apropriados é crucial para garantir medições precisas e confiáveis. A seguir, discutiremos as situações em que a calibração deve ser realizada para manter a eficácia dos instrumentos.
1. Intervalos Regulares: A calibração deve ser realizada em intervalos regulares, de acordo com as recomendações do fabricante, as demandas do setor e a frequência de uso. Para a maioria dos manômetros, a calibração anual é uma prática comum, mas em ambientes críticos, pode ser necessário calibrar a cada seis meses ou até mesmo trimestralmente.
2. Após Exposição a Condições Extremas: Se um manômetro foi exposto a condições extremas de temperatura, umidade ou pressão que estão além dos parâmetros normais de operação, ele deve ser calibrado. Essas condições podem afetar as características mecânicas ou elétricas do instrumento, resultando em leituras imprecisas.
3. Caso de Sustentação de Danos: Caso um manômetro apresente danos visíveis ou sinais de desgaste, como rachaduras, corrosão ou vazamentos, ele deve ser retirado de operação e calibrado após os reparos. Isso é importante para garantir que o instrumento funcione corretamente e forneça dados precisos.
4. Quando as Leituras Forem Inconsistentes: Se um manômetro começar a exibir leituras inconsistentes ou fora das especificações normais, deve-se proceder à calibração imediatamente. A identificação de erros nas medições pode evitar problemas sérios em aplicações sensíveis à pressão.
5. Mudanças de Localização: Se o manômetro for transferido para um novo local que possua condições ambientais diferentes, é recomendável realizar uma calibração. Mudanças na pressão atmosférica, temperatura, umidade ou vibração podem impactar sua precisão de operação.
6. Após Manutenção ou Reparo: Quando um manômetro é submetido a manutenção, ajustes ou reparos significativos, a calibração é essencial para assegurar que ele retorne ao seu estado funcional apropriado. Isso garante que qualquer ajuste realizado não comprometa as medições futuras.
7. Como Requisito Normativo: Algumas indústrias estão sujeitas a normas específicas que exigem calibrações periódicas e documentação confirmando a precisão dos instrumentos. É fundamental estar ciente dessas regulamentações e cumpri-las rigorosamente.
Em resumo, a calibração de manômetros deve ser uma prática contínua e proativa. Seguir essas diretrizes ajuda a manter a precisão das medições, assegurando a segurança e a eficiência em processos industriais críticos.
A calibração de manômetros é uma prática essencial para garantir a precisão e a confiabilidade das medições de pressão em diversos ambientes industriais.
Ao compreender a importância da calibração, os tipos de manômetros e as necessidades específicas de manutenção, é possível implementar processos que asseguram a qualidade e a segurança operacional.
A regularidade na calibração, aliada a boas práticas de manutenção, minimiza riscos e maximiza a eficiência dos sistemas, resultando em operações mais seguras e produtivas.
Manter registros detalhados e estar atento às condições de uso dos manômetros são passos cruciais para um desempenho otimizado.
Investir tempo e recursos na calibração e na manutenção dos manômetros é um passo essencial para qualquer organização que busca excelência em suas operações.