Inspeção de Tubulações e Dutos Industriais: Importância e Métodos
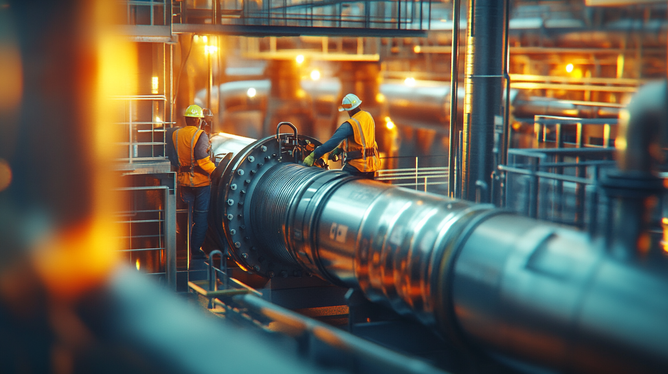
Por: Walter - 21 de Dezembro de 2024
A inspeção de tubulações e dutos industriais é fundamental para garantir a segurança e eficiência operacional em ambientes industriais. Este processo identifica falhas ocultas, prevenindo acidentes e melhorando a performance dos sistemas. Neste artigo, iremos explorar a importância dessa prática, os métodos utilizados e as tecnologias disponíveis, além de discutir como a manutenção adequada pode maximizar a vida útil das instalações. Continue lendo e descubra como otimizar sua operação industrial por meio de uma inspeção eficaz.
Importância da Inspeção de Tubulações e Dutos Industriais
A inspeção de tubulações e dutos industriais desempenha um papel vital na manutenção da segurança e eficiência de operações em diversas indústrias, incluindo petróleo, gás, química e alimentícia. Equipamentos como tubulações e dutos apresentam riscos significativos, e a sua inspeção regular é crucial para evitar acidentes, danos materiais e até mesmo perdas de vidas. Neste artigo, vamos detalhar a importância dessa prática, abordando os principais benefícios que a inspeção proporciona.
1. Prevenção de Acidentes
A principal razão para realizar a inspeção de tubulações e dutos industriais é a prevenção de acidentes. Falhas estruturais, vazamentos e rupturas podem causar acidentes graves, incluindo explosões e incêndios. A inspeção regular permite a identificação precoce de problemas, como corrosão, fissuras e desgastes, reduzindo significativamente o risco de incidentes. Uma única falha em um sistema de tubulação pode levar a consequências desastrosas, não apenas para os trabalhadores, mas também para o meio ambiente e a comunidade.
2. Manutenção da Conformidade Regulamentar
A maioria das indústrias operam sob rigorosas normas e regulamentações de segurança, que exigem a inspeção regular de tubulações e dutos. A não conformidade pode resultar em multas pesadas, penalizações legais e até mesmo a suspensão das operações. Realizar inspeções regulares garante que a empresa esteja em conformidade com as normas estabelecidas, protegendo-a contra possíveis sanções legais. Os relatórios de inspeção são essenciais para demonstrar a conformidade perante órgãos reguladores.
3. Aumento da Vida Útil do Equipamento
A inspeção regular de tubulações e dutos industriais permite a detecção e correção de problemas antes que eles se tornem críticos. Isso não apenas reduz o risco de falhas catastróficas, mas também pode aumentar a vida útil do equipamento. Quando problemas são abordados em suas fases iniciais, as empresas podem evitar substituições dispendiosas e prolongar a vida útil dos sistemas de tubulação. A manutenção preventiva, que inclui a inspeção regular, é uma estratégia eficaz para maximizar o retorno sobre o investimento em infraestrutura industrial.
4. Redução de Custos Operacionais
Embora a implementação de um programa de inspeção possa envolver custos iniciais, a longo prazo, essa prática pode resultar em economias significativas. A deteção precoce de problemas pode evitar reparos caros e paradas não programadas, que podem impactar fortemente na produtividade e nos lucros de uma empresa. Além disso, sistemas que operam de forma eficiente e segura reduzem os custos com energia e manutenção. Portanto, investir na inspeção de tubulações e dutos não é apenas uma questão de segurança, mas também uma estratégia financeira inteligente.
5. Proteção do Meio Ambiente
Os vazamentos de produtos químicos e fuel oil a partir de tubulações deterioradas podem ter impactos devastadores ao meio ambiente. A inspeção regular ajuda a mitigar essa ameaçadora realidade, permitindo a identificação de vazamentos antes que eles causem danos ao ecossistema. Além da responsabilidade ambiental, essa proatividade também reflete positivamente na imagem corporativa da empresa, que demonstra seu compromisso com a sustentabilidade e a proteção ao ambiente.
6. Melhoria da Eficiência Operacional
A eficiência operacional pode ser aprimorada com inspeções regulares e eficazes de tubulações. Sistemas otimizados e livres de problemas operam de maneira mais suave e eficaz, resultando em maior produtividade e menores interrupções. Todos os componentes de um sistema industrial devem funcionar em conjunto, e a manutenção preventiva assegura que esses componentes estejam em boas condições. Dessa forma, as empresas podem assegurar que seus processos operacionais sejam contínuos e livres de falhas.
7. Formação de Profissionais Capacitados
A realização de inspeções regulares também promove a formação e conscientização dos profissionais envolvidos na operação e manutenção dos sistemas de tubulação. A capacitação contínua desses profissionais é essencial para reconhecer, avaliar e mitigar riscos de forma eficaz. Ao preparar a equipe para executar inspeções detalhadas e relatar suas descobertas, a empresa fortalece sua cultura de segurança e comprometimento com boas práticas operacionais.
8. Tecnologias em Inspeção de Tubulações
A tecnologia está transformando o modo como a inspeção de tubulações e dutos industriais é realizada. Ferramentas como drones, câmeras infravermelhas e sensores de vibração têm permitido inspeções mais rápidas e eficientes. Tecnologia de ultrassom e radiografia são outros métodos que proporcionam uma visão interna das tubulações, detetando falhas que não seriam visíveis a olho nu. A adoção dessas tecnologias não apenas melhora a precisão das inspeções, mas também facilita a coleta de dados para análises futuras.
9. Exemplos de Inspeção Eficaz
Casos de sucesso comprovam a eficácia das inspeções de tubulações e dutos. Empresas que implementaram programas robustos de inspeção têm conseguido evitar acidentes sérios e reduzir os custos operacionais pelas razões já mencionadas. Além disso, operadoras de petróleo que utilizam tecnologia avançada para monitorar suas tubulações têm relatado uma melhora significativa em sua eficiência energética, resultando em benefícios tanto financeiros quanto ambientais.
10. Conclusão: O Valor da Inspeção Regular
Em suma, a inspeção de tubulações e dutos industriais é uma prática essencial que traz inúmeros benefícios. Desde a prevenção de acidentes até a melhoria da eficiência e a proteção ambiental, os pontos discutidos nesta seção mostram que essa prática não deve ser encarada como um gasto, mas sim como um investimento vital para a segurança e sucesso de qualquer operação industrial. A conscientização da importância das inspeções regulares é fundamental para adotá-las, impactando não apenas a empresa mas também a sociedade como um todo.
Métodos Comuns de Inspeção de Tubulações e Dutos
A inspeção de tubulações e dutos é um aspecto crucial da manutenção industrial. Com o avanço das tecnologias e a crescente necessidade de segurança e eficiência, uma variedade de métodos de inspeção está disponível. Cada método possui suas próprias vantagens e desvantagens, e a escolha do mais adequado depende das condições específicas de cada sistema e do tipo de material em questão. Neste artigo, abordaremos os métodos mais comuns de inspeção utilizados em tubulações e dutos industriais.
1. Inspeção Visual
A inspeção visual é uma das formas mais simples e diretas de avaliar a condição de tubulações e dutos. Este método envolve a observação direta das superfícies, permitindo a identificação de rachaduras, corrosão e outros danos. Embora a inspeção visual possa não revelar falhas internas, é uma excelente maneira de detectar problemas óbvios.
Embora simples, essa técnica requer treinamento adequado para que os inspetores saibam o que procurar. É essencial que sejam familiarizados com os sinais de desgaste e com as normas de segurança relacionadas ao equipamento que estão inspecionando. A inspeção visual é frequentemente utilizada como um primeiro passo antes de métodos mais específicos e intrusivos.
2. Inspeção por Ultrassom
A tecnologia de ultrassom é amplamente utilizada na inspeção de tubulações e dutos, especialmente em materiais metálicos. Este método utiliza ondas sonoras de alta frequência para determinar a espessura das paredes do tubo e identificar a presença de corrosão ou outros tipos de desgaste.
A inspeção por ultrassom é eficaz porque pode penetrar no material e fornecer medições precisas. O equipamento é portátil e pode ser utilizado em campo, permitindo avaliação sem necessidade de desmontar sistemas complexos. Contudo, é necessário que os operadores sejam bem treinados para interpretar os resultados e garantir a precisão das medições.
3. Inspeção por Radiografia
A radiografia é uma técnica que utiliza radiação ionizante para criar imagens das tubulações e dos dutos. Este método permite visualizar o interior das tubulações e detectar falhas ocultas, como fissuras, porosidade e inclusões de materiais indesejados.
Uma das principais vantagens da radiografia é a capacidade de oferecer imagens de alta qualidade que permitem uma análise detalhada. No entanto, devido ao uso de radiação, essa técnica requer precauções rigorosas e conformidade com regulamentações de segurança. Além disso, é necessário habilitar pessoal qualificado para operar o equipamento e interpretar as imagens obtidas.
4. Inspeção por Tomografia
A tomografia é uma técnica avançada que utiliza múltiplas imagens em diferentes ângulos para produzir uma visão tridimensional da tubulação. Embora ainda não seja tão comum quanto os métodos anteriormente mencionados, a tomografia tem ganhado popularidade devido à sua capacidade de produzir imagens integradas e detalhadas.
Ao contrário da radiografia, que pode exigir mais tempo e esforço na interpretação, a tomografia pode mostrar interações complexas dentro do material. Contudo, o uso dessa técnica pode ser dispendioso e requer equipamentos sofisticados e operadores treinados.
5. Inspeção por Câmeras Endoscópicas
As câmeras endoscópicas são uma ferramenta prática para visualizar o interior de tubulações e dutos. Essa técnica envolve a inserção de uma câmera miniature na tubulação, permitindo a visualização de como as condições internas afetam o desempenho do sistema.
Uma boa aplicação para as câmeras endoscópicas é avaliar o acúmulo de detritos, corrosão e outras anomalias. Estas câmeras podem ser combinadas com iluminação LED para fornecer imagens nítidas, mesmo em ambientes com pouca luz. Esse método é menos invasivo e permite a documentação visual, que pode ser útil para relatórios e análises históricas.
6. Métodos de Detecção por Pressão
A detecção de pressão é um método utilizado para verificar a integridade de sistemas pressurizados. Este teste pode identificar vazamentos que não são evidentes em uma inspeção visual ou mesmo com métodos mais técnicos. O sistema é pressurizado e monitorado ao longo do tempo para verificar se há quedas de pressão, indicando a presença de vazamentos.
Os testes de pressão são particularmente importantes em instalações de gás e petróleo, onde a segurança é uma preocupação primordial. No entanto, a utilização desse método deve ser feita por profissionais qualificados, já que a pressão inadequada pode causar danos à tubulação ou resultar em situações perigosas.
7. Inspeção por Drones
O uso de drones na inspeção de tubulações tem se tornado cada vez mais comum, especialmente para sistemas extensos e de difícil acesso. Equipados com câmeras de alta resolução e sensores térmicos, os drones podem fornecer imagens aéreas detalhadas e detectar anomalias que não seriam visíveis a partir do solo.
Além disso, os drones podem realizar inspeções em áreas perigosas, como locais de construção ou instalações em altura, reduzindo os riscos para os operadores humanos. Apesar de sua eficiência, os drones ainda precisam de uma equipe de profissionais qualificados para operar e interpretar os dados coletados.
8. Inspeção Não Destrutiva (END)
A Inspeção Não Destrutiva (END) é um conjunto de técnicas que permite avaliar a estrutura de tubulações e dutos sem causar danos ao material. Isso é especialmente importante em sistemas que não podem ser desmontados ou interrompidos para manutenção. Relacionadas à END estão as técnicas de ultrassom, radiografia e inspeção por líquidos penetrantes, que são todas utilizadas para avaliar a integridade estrutural.
Uma das principais vantagens da inspeção não destrutiva é que ela permite realizar inspeções regulares sem interromper o funcionamento do sistema. Este contínuo monitoramento contribui para a manutenção preditiva, permitindo que problemas sejam identificados e corrigidos antes de se tornarem falhas críticas.
9. Análise de Dados e Manutenção Preditiva
Com o avanço da tecnologia, a coleta de dados em tempo real durante as inspeções tem se tornado uma prática comum. Sensores instalados nas tubulações podem monitorar pressão, temperatura e outros parâmetros, enviando esses dados para uma plataforma central. Isso permite análises preditivas, que podem prever falhas antes que ocorram e programar manutenções de forma mais estratégica.
Essa análise de dados não apenas melhora a segurança, mas também ajuda a otimizar a eficiência das operações. A manutenção preditiva proporciona uma abordagem mais confiante em relação ao planejamento e execução de manutenção, economizando tempo e recursos para a empresa.
10. Conclusão
Em resumo, os métodos de inspeção de tubulações e dutos são variados e cada um possui suas próprias aplicações, vantagens e limitações. A escolha do método a ser utilizado deve ser baseada nas necessidades específicas do sistema, nas condições do ambiente e no tipo de material da tubulação. Na maioria das vezes, uma combinação de métodos é a solução ideal para garantir a integridade e segurança das operações industriais. À medida que a tecnologia avança, novas e melhores técnicas de inspeção continuam a surgir, contribuindo para um futuro mais seguro e eficiente para as tubulações e dutos industriais.
Tecnologia Utilizada na Inspeção Industrial
A inspeção industrial é um componente essencial para garantir a integridade e segurança das operações em ambientes industriais. Com o avanço da tecnologia, uma gama diversificada de ferramentas e técnicas foram desenvolvidas para otimizar e aprimorar esse processo. Neste artigo, vamos explorar as principais tecnologias utilizadas na inspeção de tubulações e dutos industriais, detalhando suas funcionalidades, aplicações e benefícios.
1. Ultrassom
A tecnologia de ultrassom é amplamente utilizada na inspeção de diferentes materiais, principalmente metais. A inspeção por ultrassom envolve a geração de ondas sonoras de alta frequência que são transmitidas através da superfície do material. Quando essas ondas encontram uma descontinuidade, como uma fissura ou corrosão, uma parte da energia é refletida de volta, permitindo a identificação de falhas.
A inspeção ultrassônica é eficaz em medir a espessura das paredes das tubulações, ajudando a identificar a corrosão localizada. Este método é frequentemente utilizado em instalações de petróleo e gás, além de estruturas de pressão e caldeiras. A precisão e a velocidade da inspeção ultrassônica, aliadas ao seu baixo custo operacional, fazem dela uma escolha popular na análise da integridade estrutural.
2. Radiografia
A radiografia é uma tecnologia de inspeção que utiliza radiação ionizante para criar imagens detalhadas da estrutura interna de tubulações e dutos. Esta técnica permite visualizar falhas ocultas, como porosidades, fissuras e inclusões de materiais, que podem comprometer a integridade do sistema.
O processo de radiografia envolve a exposição do material à radiação, que passa através de diferentes densidades do material, criando uma imagem em um filme fotográfico ou detector digital. Embora a radiografia produza imagens de alta qualidade, é importante destacar que o manuseio deve ser realizado por profissionais treinados devido ao risco associado à exposição à radiação.
3. Câmeras Térmicas
A tecnologia de câmeras térmicas tem se tornado cada vez mais popular na inspeção industrial. Essas câmeras capturam a radiação infravermelha emitida pelos objetos, permitindo a visualização de variações de temperatura em tubulações e dutos. A análise térmica é uma técnica eficaz para detectar vazamentos de gás e fluidos, além de identificar problemas de isolamento e superaquecimento.
O uso de câmeras térmicas é vantajoso, pois permite a inspeção de grandes áreas em pouco tempo, sem a necessidade de contato físico. Além disso, as imagens térmicas geradas podem ser facilmente documentadas e compartilhadas para fins de análise e relatórios, facilitando a comunicação dos resultados para a equipe de manutenção.
4. Endoscopia Industrial
As câmeras endoscópicas são uma ferramenta muito útil na inspeção de tubulações, especialmente aquelas de pequeno diâmetro ou de difícil acesso. Estas câmeras são inseridas nas tubulações e transmitem imagens em tempo real, permitindo a visualização direta das condições internas.
As câmeras endoscópicas são uma opção de baixo custo e oferecem uma solução prática para a inspeção visual detalhada. A tecnologia está disponível em diferentes formatos, incluindo modelos portáteis, que podem ser usados em campo, e modelos mais avançados, que podem permitir a gravação e a análise dos dados coletados.
5. Drones
O uso de drones na inspeção de tubulações e dutos industriais é uma tendência crescente que vem revolucionando a forma como as inspeções são realizadas. Equipados com câmeras de alta resolução e sensores, os drones podem fornecer imagens aéreas detalhadas e capturar dados em locais de difícil acesso, como terrenos acidentados ou áreas em altura.
Os drones oferecem a vantagem de realizar a inspeção de maneira rápida e segura, reduzindo o risco de acidentes para os trabalhadores. Além disso, a tecnologia dos drones permite a documentação visual eficiente do estado das instalações, que pode ser compartilhada instantaneamente com a equipe de manutenção para análise e planejamento de ações corretivas.
6. Sensores de Vibração
Os sensores de vibração são dispositivos utilizados para monitorar o desempenho de máquinas e equipamentos em tempo real. Na inspeção industrial, esses sensores podem ser aplicados para identificar problemas em tubulações e dutos, como desalinhamentos, desequilíbrios e falhas nas conexões.
A monitorização contínua das vibrações permite a detecção precoce de falhas, potencialmente economizando tempo e recursos. Os dados coletados pelos sensores podem ser analisados e utilizados para programar manutenções preditivas, garantindo que as intervenções ocorram antes que problemas sérios se desenvolvam.
7. Metodologia de Inspeção no Local (On-Site)
A metodologia de inspeção no local utiliza uma combinação de tecnologias e práticas específicas para a avaliação da integridade de tubulações e dutos. Técnicas como a visualização em 3D, utilizadas em conjunto com métodos de imagem, ajudam a criar uma representação precisa do sistema. Essa abordagem permite que os engenheiros e técnicos consigam uma visão abrangente do que se passa nas instalações, auxiliando na tomada de decisões informadas quanto à manutenção e reparo.
A inspeção on-site pode incluir tanto a aplicação de métodos tradicionais, como teste de pressão e medições físicas, quanto o uso de tecnologias de ponta, como sensores e imagens térmicas. Essa flexibilidade permite que equipes de manutenção adaptem suas abordagens de acordo com as necessidades específicas de cada sistema e ambiente.
8. Análise de Dados e Inteligência Artificial
Com o aumento do uso de sensores e dispositivos conectados, a análise de dados e a inteligência artificial (IA) estão se tornando cada vez mais relevantes na inspeção industrial. A coleta de dados operacional em tempo real pode ser analisada para identificar padrões e prever falhas antes que elas ocorram, permitindo uma abordagem proativa para a manutenção.
A IA pode, por exemplo, otimizar a programação de manutenção com base em dados históricos, prever a vida útil do equipamento e prever quando uma falha pode ocorrer. Isso proporciona mais segurança e confiabilidade nos processos, além de gerenciar melhor os recursos disponíveis, garantindo um funcionamento contínuo e eficiente das instalações industriais.
9. Inspeção Não Destrutiva com líquidos penetrantes
A inspeção não destrutiva por líquidos penetrantes é um método econômico e altamente eficaz para detectar descontinuidades em superfícies metálicas. Este método envolve a aplicação de um líquido penetrante na superfície do material, que infiltra-se em falhas presentes, como fissuras ou poros. Após um período de espera, um desenvolvedor é aplicado, que causa a coloração das falhas, permitindo a sua visualização.
Este método é amplamente utilizado na indústria, especialmente na área de manutenção de tubulações, para garantir que os materiais estejam em conformidade com as especificações de segurança. A inspeção com líquidos penetrantes é preferível em situações em que os métodos fotográficos ou de ultrassom podem ser inadequados, proporcionando uma forma eficaz de monitorar a integridade dos materiais.
10. Conclusão
As tecnologias de inspeção industrial têm avançado significativamente, proporcionando novas oportunidades para garantir a integridade e segurança de tubulações e dutos. Cada método possui uma gama de aplicações e benefícios, permitindo que as empresas escolham a melhor abordagem para suas necessidades específicas. O uso de uma combinação de tecnologias pode ser a chave para maximizar a eficiência dos processos de inspeção e assegurar um desempenho ideal nas operações industriais. À medida que as inovações tecnológicas continuam a evoluir, é evidente que a inspeção industrial entrará em uma nova era, onde segurança, eficiência e sustentabilidade estarão em primeiro plano.
Manutenção e Reparos Após a Inspeção
A manutenção e os reparos de tubulações e dutos industriais são etapas cruciais que seguem a inspeção. Após a identificação de falhas ou desgastes, as empresas enfrentam o desafio de implementar as ações corretivas necessárias para garantir a segurança e eficácia de suas operações. O processo não se limita apenas a corrigir problemas, mas também envolve o planejamento adequado e a implementação de uma manutenção preventiva que possa prolongar a vida útil dos sistemas. Neste artigo, exploraremos a importância da manutenção e reparos após a inspeção, suas práticas recomendadas e as melhores estratégias de implementação.
1. A Importância da Manutenção Corretiva
Após uma inspeção, é imperativo abordar as falhas identificadas de forma rápida e eficaz. A manutenção corretiva é a prática de reparar ou substituir componentes que foram diagnosticados como falhos. Ignorar esses problemas pode levar a falhas catastróficas, que podem resultar em acidentes, paradas de produção e custos adicionais. Além disso, situações de emergência podem envolver riscos à vida, danos ao meio ambiente e prejuízos financeiros significativos para a empresa.
Realizar a manutenção corretiva imediatamente após a inspeção, quando necessário, ajuda a preservar a integridade das operações e assegurar um ambiente de trabalho mais seguro. A rapidez nas decisões e na execução de reparos é, portanto, fundamental.
2. Planejamento da Manutenção
Uma parte essencial das operações de manutenção é o planejamento adequado. Após a inspeção, é crucial documentar os resultados e determinar o escopo dos reparos necessários. Um planejamento cuidadoso ajuda a priorizar as ações com base na gravidade dos problemas identificados, permitindo a alocação eficiente de recursos, tempo e mão de obra.
O planejamento deve incluir as seguintes etapas:
- Documentação: Registro detalhado dos resultados da inspeção, incluindo fotos, medições e recomendações específicas.
- Classificação das Falhas: Avaliação da gravidade de cada problema para determinar prioridades de ação.
- Definição de Recursos: Estimativa dos recursos necessários, incluindo peças de reposição, equipamentos e mão de obra.
- Cronograma: Estabelecimento de um cronograma realista para a execução dos reparos.
Utilizar ferramentas de gestão de manutenção, como sistemas de gerenciamento de manutenção computadorizada (CMMS), pode facilitar o processo de planejamento e ajudar a manter um registro organizado das atividades realizadas.
3. Tipos de Manutenção
A manutenção pode ser classificada em diferentes categorias, cada uma com seu conjunto de protocolos e práticas específicas:
Manutenção Corretiva: Refere-se à reparação de falhas que já ocorreram. Isso pode incluir a substituição de peças danificadas e a execução de serviços de reparo. A manutenção corretiva é uma resposta a problemas identificados durante a inspeção.
Manutenção Preventiva: Esta abordagem envolve ações programadas para prevenir falhas antes que ocorram. A manutenção preventiva é essencial para garantir que os sistemas permaneçam em bom estado operacional. A prática regular de manutenção preventiva pode reduzir a necessidade de correções inesperadas e dispendiosas.
Manutenção Preditiva: Com o avanço das tecnologias de monitoramento, a manutenção preditiva se torna cada vez mais comum. Este método envolve a monitorização contínua de condições operacionais e a previsão de falhas antes que elas ocorram, permitindo intervenções programadas para evitar paradas não planejadas.
Além dessas opções, a implementação de um programa de manutenção integral que combine elementos de cada um desses métodos pode ser promovida, trazendo mais eficiência ao processo.
4. Peças de Reposição e Materiais
A escolha de peças de reposição e materiais adequados é crucial para a eficácia de qualquer reparo. Após uma inspeção, é preciso garantir que os componentes utilizados para os reparos sejam compatíveis com o sistema e atendam aos padrões de qualidade. O uso de partes de baixa qualidade pode resultar em falhas adicionais e comprometer a segurança da operação.
Além disso, a escolha de materiais deve considerar fatores como:
- Resistência à Corrosão: Materiais que conseguem resistir a ambientes agressivos prolongam a vida útil dos sistemas.
- Compatibilidade Química: Peças que são adequadas para o tipo específico de fluido transportado minimizam o risco de vazamentos.
- Eficiência na Instalação: Peças que são fáceis de instalar reduzem o tempo de paralisação do sistema.
A tendência atual é buscar fornecedores confiáveis que ofereçam garantias e assegurem a qualidade dos produtos fornecidos.
5. Treinamento e Capacitação da Equipe
Um fator crítico para o sucesso da manutenção e reparos é ter colaboradores bem treinados e capacitados. A equipe encarregada de realizar os serviços de reparo deve estar ciente das melhores práticas de segurança e seguir as diretrizes de procedimentos adequadas.
O treinamento deve incluir:
- Procedimentos de Segurança: Técnicas de manuseio seguro de ferramentas e equipamentos.
- Conhecimento Técnico: Compreensão do funcionamento das tubulações e dutos, além do diagnóstico e reparo de falhas.
- Novas Tecnologias: Capacitar a equipe para operar tecnologias emergentes que possam ser aplicadas nas inspeções e manutenções.
Oferecer treinamento regular garante que a equipe esteja atualizada sobre novos produtos, práticas e tecnologias da indústria, resultando em atividades de manutenção mais eficientes e seguras.
6. Relatórios e Documentação
A documentação é uma parte vital do processo de manutenção após a inspeção. É fundamental manter registros precisos de todas as atividades realizadas, incluindo inspeção, reparos e manutenções preventivas. Este registro não apenas auxilia na gestão de ativos, mas também fornece um histórico valioso para futuras inspeções e manutenção.
Os relatórios devem incluir:
- Resultados de Inspeção: Detalhes sobre falhas identificadas e sua gravidade.
- Medidas Corretivas: O que foi feito para corrigir os problemas.
- Recomendações: Sugestões para futuras manutenções e inspeções.
- Data e Responsável: Informar quem executou os serviços e quando foram realizados.
Além de garantir a transparência e a organização, a documentação adequada permite análises cronológicas que podem levar a melhorias contínuas nos processos industriais.
7. Análise de Causa Raiz
Após a conclusão dos reparos, é vital analisar a causa raiz dos problemas identificados para evitar recorrências. A análise da causa raiz é uma abordagem sistemática para identificar os fatores que contribuíram para a falha, a fim de prevenir a repetição do problema no futuro.
Essa análise pode envolver questionamentos como:
- Quais condições levaram à falha?
- O que poderia ter sido feito para evitar a falha?
- Existem padrões que indicam que o problema pode ocorrer novamente?
Compreender as causas subjacentes permite a implementação de soluções eficazes, melhorando a confiabilidade dos sistemas de tubulação e dutos no longo prazo.
8. Compromisso com a Melhoria Contínua
Após a realização da manutenção corretiva e a implementação de todas as etapas acima, as empresas devem se comprometer com a melhoria contínua de seus processos de manutenção. Esse compromisso deve ser uma parte da cultura organizacional e se refletir em todos os níveis da empresa.
Isso pode incluir a realização de reuniões periódicas de equipe para discutir os resultados de manutenções recentes, compartilhar lições aprendidas e identificar oportunidades de melhoria. Além disso, a busca por novas tecnologias e técnicas deve ser uma prioridade, para assegurar que a empresa esteja sempre na vanguarda da eficiência e segurança.
9. Considerações Finais
A manutenção e os reparos após a inspeção são etapas indispensáveis para garantir a segurança e eficiência das operações em ambientes industriais. O processo demanda cuidadoso planejamento, execução eficiente e integração de práticas de melhoria contínua para assegurar que os sistemas de tubulação e dutos permaneçam em boas condições operacionais.
Investir em capacitação, documentação e análise de causa raiz efetiva permite não apenas uma adaptação adequada às necessidades atuais, mas também previne falhas recorrentes. A abordagem proativa na manutenção assegura que os ativos industriais sejam geridos de maneira mais eficiente, contribuindo para a longevidade dos equipamentos e a segurança no local de trabalho.
É essencial que as empresas reconheçam a importância de uma estratégia de manutenção robusta e integrada, que contemple não apenas as ações corretivas, mas também um forte componente de manutenção preventiva e preditiva. Assim, estará melhor preparada para os desafios que o ambiente industrial atual apresenta.
Após explorar a importância da inspeção de tubulações e dutos industriais, bem como os métodos e tecnologias envolvidos, fica evidente que esse processo é imprescindível para a segurança e eficiência das operações. A identificação precoce de falhas não apenas previne acidentes, mas também contribui para a melhoria contínua dos sistemas. A manutenção e os reparos realizados após a inspeção desempenham um papel crucial na preservação da integridade estrutural e operacional das instalações. Adotar uma abordagem proativa, que engloba inspeções regulares, técnicas de manutenção adequadas e o uso de tecnologias modernas, é essencial para maximizar a vida útil dos dutos e tubulações industriais. Com isso, as empresas podem garantir não apenas a conformidade com regulamentações, mas também otimizar suas operações, levando a um ambiente de trabalho mais seguro e eficiente. Portanto, é crucial que as organizações se comprometam com práticas de manutenção eficazes, assegurando a longevidade e confiabilidade de seus sistemas.